Tools & methods
The latest technology in our design & manufacturing process to improve lead time and efficiency.
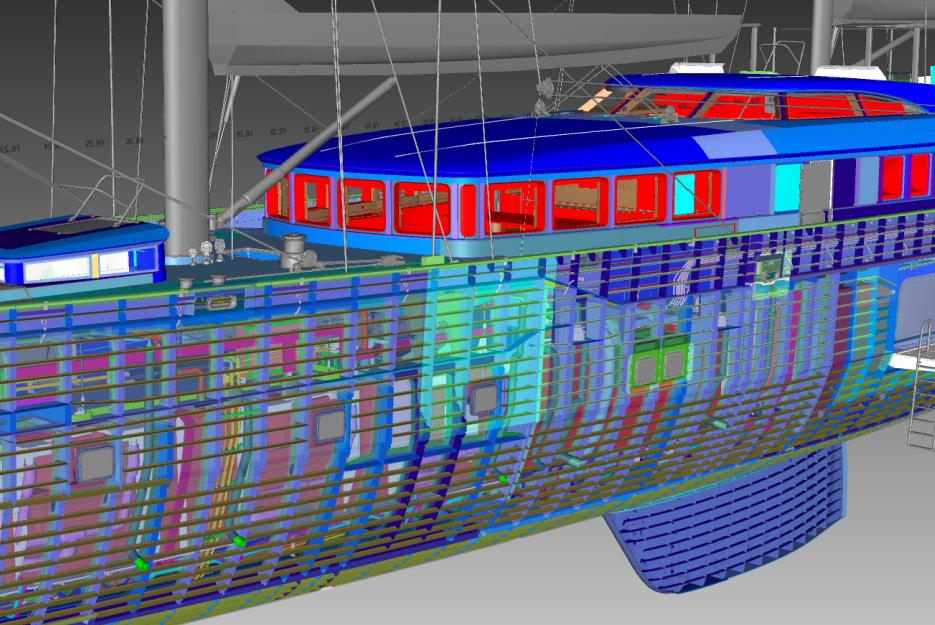
Satellite industries
“The shipyard embraced a concept known as Concurrent Design & Engineering, a method of product development based on completing processes at the same time while involving all disciplines. A related process is Stage Gating, by which a project is divided into distinct stages separated by decision points known as gates.” according to Superyacht Times article about Project 400 Sea Eagle.
“Both methodologies are commonly used in the aerospace and satellite industries with the aim of increasing time and cost efficiency while maintaining quality. ‘Basically, before starting each phase of construction we discuss what we want to deliver, what the details and implications are, and make decisions together with the departments that come after,’ explains Royal Huisman’s project manager.”
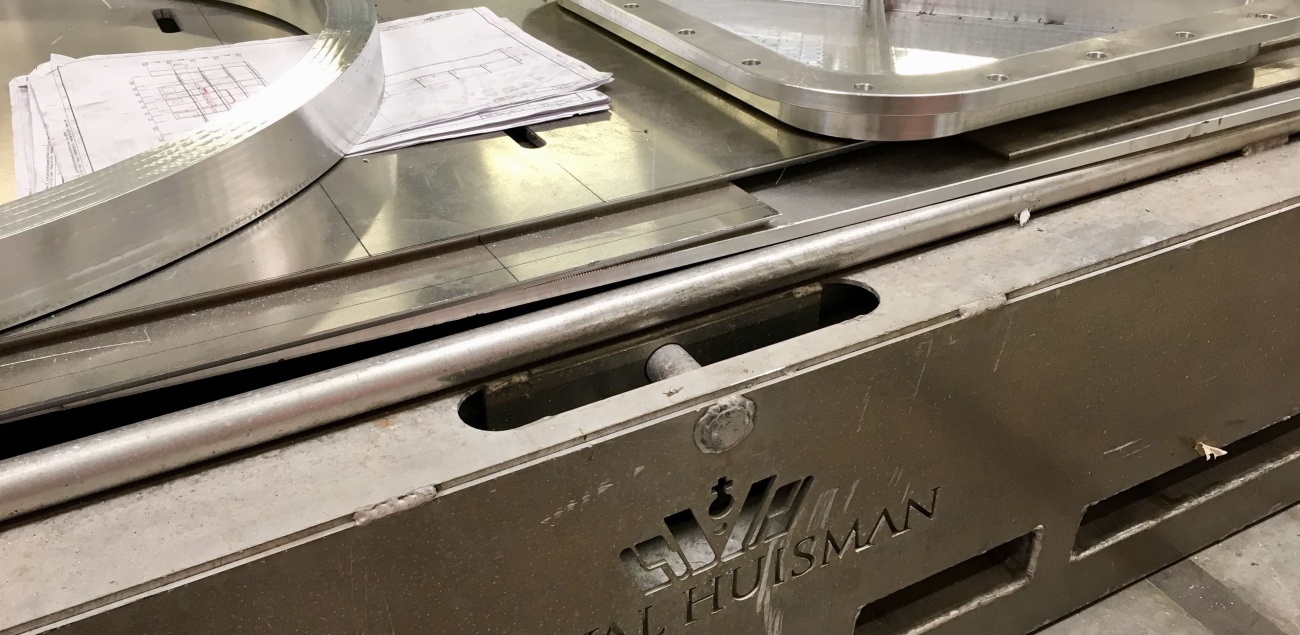
Like a flatpack from Ikea
“We also add a lot of details during the CNC milling, like perforations for deck winches instead of aligning and drilling them afterwards. It basically means more accurate and efficient assembly a bit like a flatpack from IKEA.”
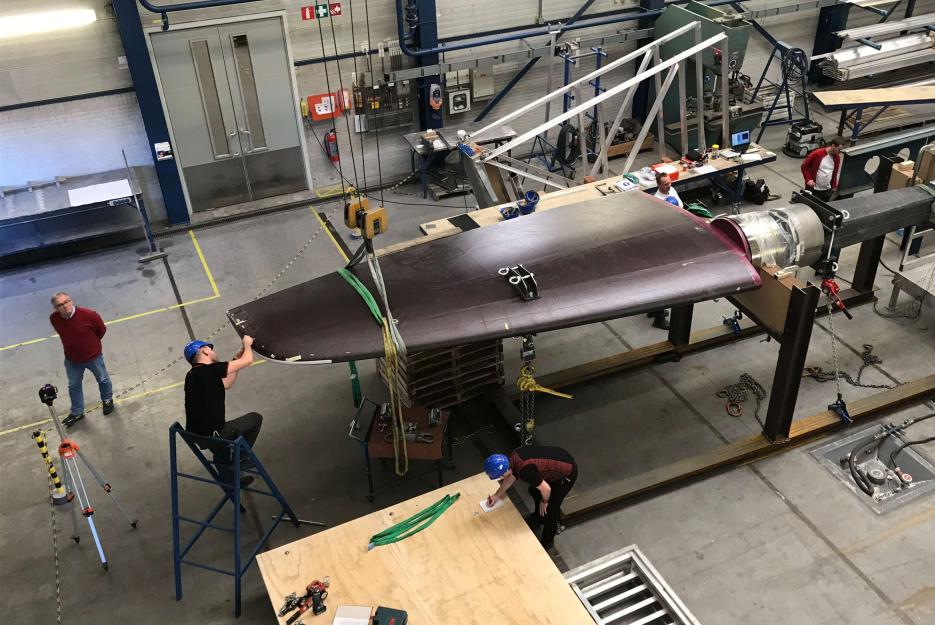
Plug-and-play
“Another production improvement has been the adoption of modular skid fabrication. Instead of installing engineering components individually, the systems are assembled within a frame or skid for plug-and-play installation.
Skids allow us to build entire systems in parallel, test them onsite and install them as complete units. With as many as 20 skids on this project – from fuel and fresh water to AC and entertainment system – it makes the whole installation process faster and more efficient.’” – From Superyacht Times article about Project 400.
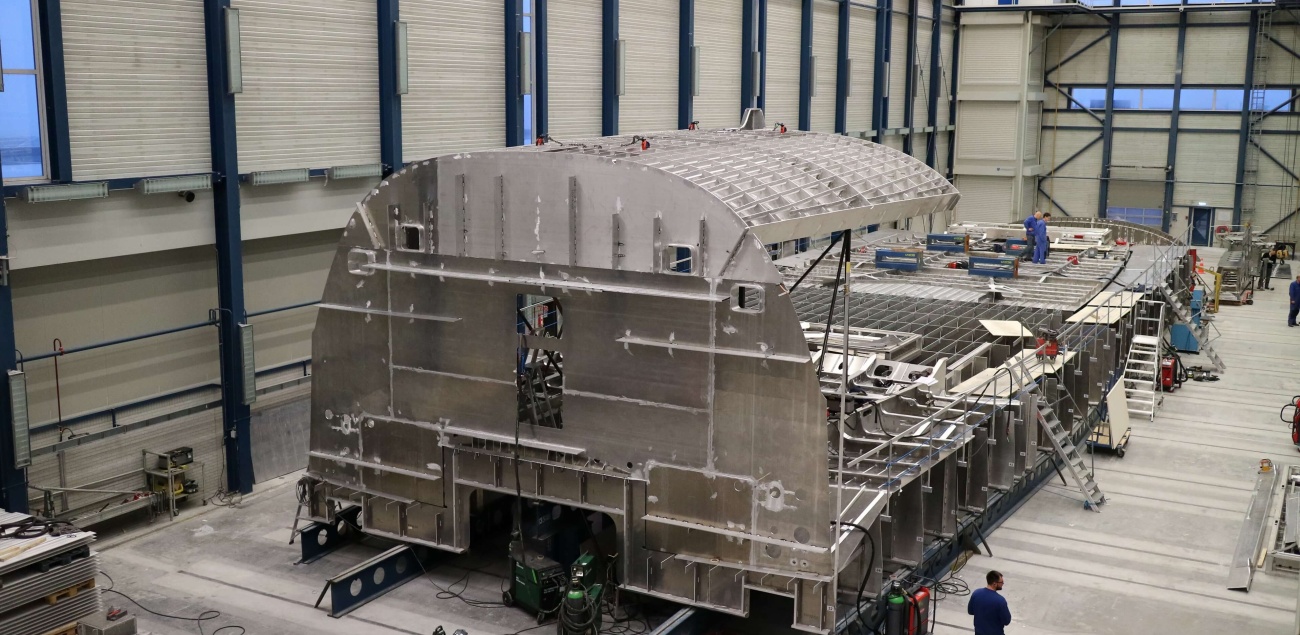
Load sensing
The XXL advanced composite rudder of Project 400 was made by sister company Rondal and equipped with load sensing technology.
rc-resize(1).jpg?resolution=935x625)
The answer is glue
The sleek design of project 400 features a superstructure made from rigid laminated glass, raising challenges in connecting it to the flexible hull without causing damage. The solution is a sophisticated glue developed by aerospace experts specifically for this purpose. While the rear of the superstructure is welded, the forward part uses this glue, allowing for up to 2cm of flex and ensuring a secure, weathertight bond. Similar flexible bonding techniques are also employed i
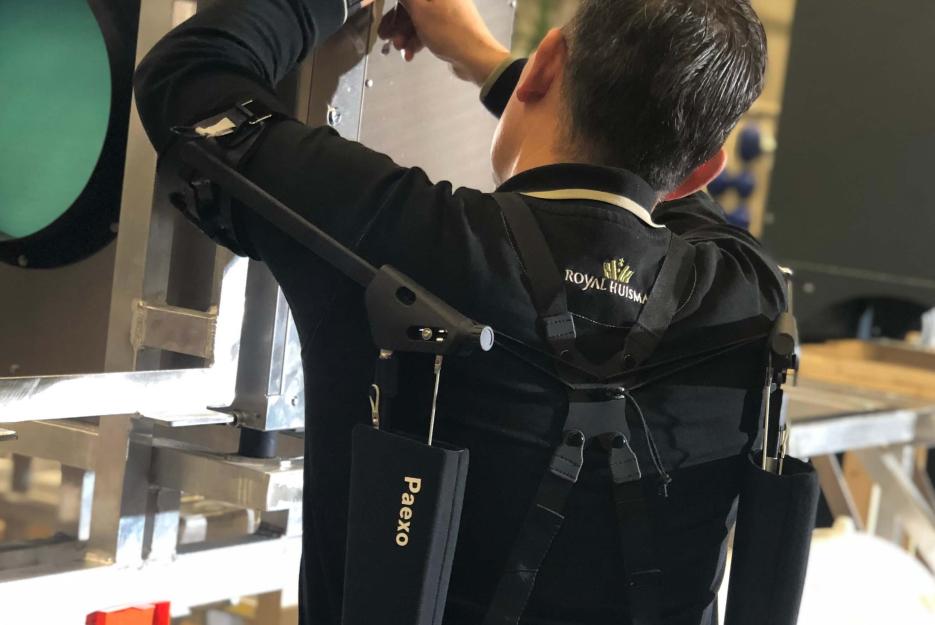
Exoskeletons
For the relieve of heavy overhead work.